Getting The Alcast Company To Work
Getting The Alcast Company To Work
Blog Article
The Basic Principles Of Alcast Company
Table of ContentsThe Main Principles Of Alcast Company The Single Strategy To Use For Alcast CompanyThe Basic Principles Of Alcast Company The smart Trick of Alcast Company That Nobody is Talking AboutSome Known Details About Alcast Company Some Ideas on Alcast Company You Need To KnowThings about Alcast Company

If you believe that a wrought alloy might be the most effective for your job, have a look at several of our short articles that describe even more regarding certain wrought alloys, such as Alloy 6061 and Alloy 6063. On the other hand, if you assume a cast alloy would certainly be much better for you, you can discover more about some cast alloys in our Alloy 380 and Alloy 383 write-ups (coming soon).
The smart Trick of Alcast Company That Nobody is Talking About
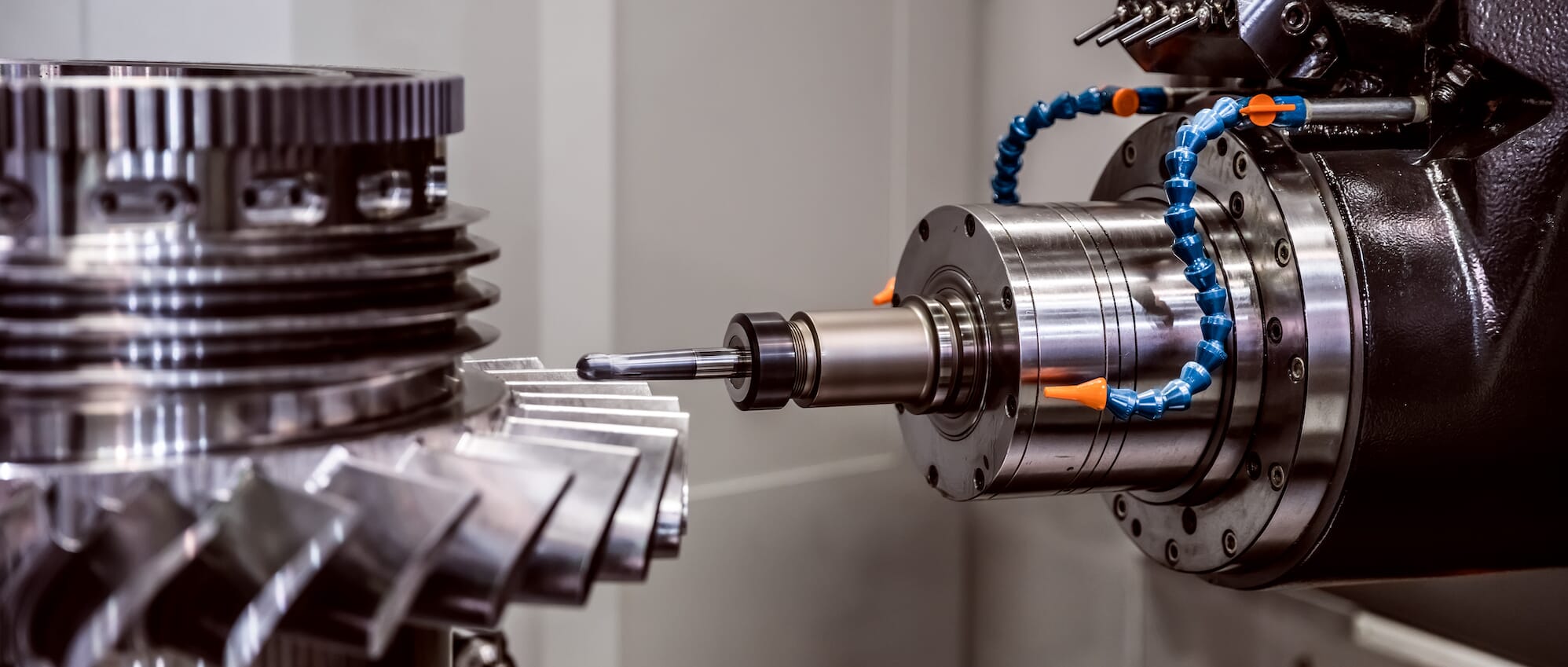
Having the experience and sector expertise to craft your spreadings for optimum manufacturing and top quality end results will certainly streamline the project. Making light weight aluminum spreading calls for a facility collection of processes to accomplish the appropriate outcomes. When determining on a brand-new aluminum foundry to partner with, ensure they have extensive industry experience and are knowledgeable concerning all facets of the light weight aluminum casting process: design, manufacturing, product evaluation, and item testing.
(https://urlscan.io/result/d4b9b54a-d6c3-4270-aa51-cae2e1e6816f/)The shop ought to additionally have a tested performance history of providing remarkable items that meet or go beyond customer assumptions. Quality assurance ought to additionally be at the top of your checklist when choosing a light weight aluminum shop. By working with a qualified factory that complies with the criteria for quality assurance, you can secure the integrity of your product and guarantee it fulfills your specifications.
The Alcast Company PDFs
By picking a firm who uses services that fulfill or surpass your product requirements, you can be certain that your job will be completed with the utmost precision and efficiency. Various components require various production techniques to cast light weight aluminum, such as sand spreading or die spreading.
Die spreading is the name provided to the process of developing complicated steel elements through usage of molds of the part, likewise referred to as passes away. The process makes use of non-ferrous steels which do not include iron, such as light weight aluminum, zinc and magnesium, because of the preferable why not try here properties of the steels such as low weight, greater conductivity, non-magnetic conductivity and resistance to corrosion.
What Does Alcast Company Do?

After the purity of the alloy is tested, passes away are produced. To prepare the passes away for spreading, it is crucial that the dies are clean, so that no deposit from previous manufacturings remain.
The pure metal, likewise referred to as ingot, is added to the heater and kept at the molten temperature of the metal, which is after that transferred to the injection chamber and injected into the die (aluminum foundry). The stress is after that preserved as the metal solidifies. Once the metal strengthens, the cooling procedure begins
The Alcast Company Diaries
The thicker the wall surface of the component, the longer the cooling time as a result of the amount of indoor steel that also needs to cool down. After the part is completely cooled down, the die halves open and an ejection mechanism pushes the part out. Adhering to the ejection, the die is shut for the next injection cycle.
The flash is the additional product that is cast during the procedure. Deburring gets rid of the smaller pieces, called burrs, after the cutting process.
Everything about Alcast Company
This verified to be an imprecise examination, due to the fact that the tester might cut into a piece and miss a location with porosity. Today, top producers utilize x-ray screening to see the entire interior of components without cutting right into them. This permits them to much more precisely approve or reject parts. To reach the finished item, there are three main alloys used as die casting material to pick from: zinc, light weight aluminum and magnesium.
Zinc is one of the most pre-owned alloys for die casting due to its reduced expense of raw materials (aluminum casting manufacturer). Its deterioration resistance also permits the components to be long lasting, and it is one of the much more castable alloys due to its lower melting point.
Alcast Company for Dummies
As pointed out, this alloy is among the most generally used, yet manufactures will, sometimes, select light weight aluminum over zinc as a result of aluminum's manufacturing benefits. Light weight aluminum is very economical and among the more flexible alloys. Aluminum is made use of for a number of different items and markets anything from home window frames to aerospace materials.
Report this page